Many companies use Manufacturing Execution Systems (MES), to control key aspects of production activities. This improves product traceability, productivity and quality. MES can effectively reduce the occurrence of errors in the process. It collects data at each step, including who operates the process, when it was completed, how long each process took, the equipment used by the process, and other parameters. In addition, it provides instant data reference for each worker and what stage the current project is in. MES can also implement functions such as equipment tracking, product serialization, labor tracking, inventory management, cost accounting, task completion notifications, and monitoring of defective products and remedial actions.
MES 2
Artificial Disadvantages
In order to fine-tune the production process in order to improve the process. Engineers need more precise and detailed data. Includes costing, WIP tracking, equipment and labor tracking, and more. By effectively digitizing data collection and thus optimizing the entire system, MES can achieve exponentially higher production efficiency. Traditional MES employ barcodes or manual data collection at all stages. However, manual data collection has large errors and it is difficult to Provide Accurate Data
RFID Manufacturing Execution System
In this context, Shanghai RFIDHY’s RFID automatic tracking data acquisition system came into being. This system can transform a traditional MES system into a real-time MES system.
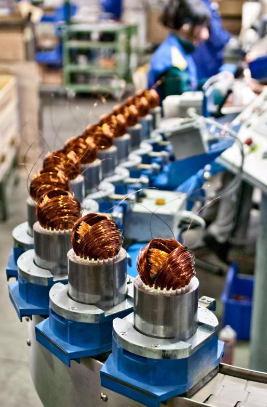
MES 1
Shanghai RFIDHY’s RFID tracking system automates data collection, including real-time reporting of raw material consumption, enabling real-time inventory updates; work-in-progress (WIP) tracking, tooling, documentation, and operator tracking. All of this information is fed into the MES, enabling real-time updates across the manufacturing floor.
Shanghai RFIDHY’s tracking system can also make MES updates more accurate. For example, when raw materials are sent from the warehouse to the assembly line, ERP can enter the data into the system as the material leaves the warehouse, and then log it again when the product arrives on the assembly line to ensure that nothing goes wrong. Because in the traditional system, the person who enters the product into the system on the assembly line may not be at the workstation, so this data cannot be entered.
More Advantages
Likewise, Shanghai RFIDHY’s RFID tracking system can automatically capture data on all tools and equipment used on the production line, passengers, documents, and even the operators of each workstation on the production line. Alerts can be issued for faulty tools, devices that have exceeded the detection time limit, and faulty files. In addition, it can flag operators online who have not completed the necessary certification or training, reminding them to update their certification information in a timely manner.
RFID can greatly enrich existing MES, improve operational efficiency, and improve product quality.
Keyword: RFIDHY Warehousing NFC tag RFID Solutions