$1.1 billion loss of machine vision
Although 72% of factories have deployed machine vision, they still lose $1.1 billion each year due to the following problems:
- Occlusion defects: 38% of defects are obscured by parts or oil
- Data silos: Pure vision systems lack 60% of upstream and downstream production data
RFID industrial tags complement the key functions of vision systems:
✔️ Underground tracking under liquid/metal
✔️ Full-link data closed loop from raw materials to quality inspection
Application: Machine vision RFID integration reshapes Industry 4.0
1.Occlusion area defect detection (UHF RFID)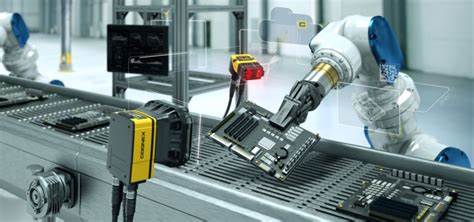
Pain point: 29% of welding defects are obscured by brackets and missed by vision systems
Solution:
- RFID spatial anchor guides ultrasonic imaging to focus on the occlusion area
- Tags store 3D welding drawings for real-time comparison by AI models
Result: Defect capture rate increased from 71% to 99.7%
2.Multi-material sorting (HF Spectral tag)
Visual limitation: PET and PP confusion results in only 82% recovery purity
Solution:
- High-frequency tag emits material characteristic frequency signal
- Visual CNN model associates spectral peak with surface texture
Result: Purity reaches 99.1%, meeting EU circular economy standards
3.Dark environment process monitoring (passive UHF sensor tag)
Risk: 34% of coating thickness fluctuations are not detected
Technical breakthrough:
UHF tag capacitive sensor measurement:
- Coating thickness (0-500 microns, error ±0.8 microns)
- Curing state (through dielectric constant analysis)
Data superimposed on visual thickness map to achieve ISO 2178/2360 dual verification
4.Cross-system data bridging (HF blockchain tag)
Data island: 73% of upstream defects are missed by visual system
Solution:
- RFID material ID is bound to visual defect map
- AI root cause analysis model associates upstream and downstream data
- Synchronize to MES/ERP to drive predictive optimization
Benefit: Overall equipment efficiency increased by 68% (OEE)
Three steps to become a machine vision-RFID leader
- Diagnosis: Use visual blind spot analysis tools to identify RFID value-added points
- Pilot: Deploy occlusion detection or high-speed tracking hybrid kit
- Pilot: Launch AI-driven defect prediction engine
Limited time software partner exclusive:
Free access to the “Vision-RFID Fusion Technology White Paper” (worth $7,500)
The first 25 will receive 100 test tags
Leave your contact detail now to get the latest price!