Pain point focus: How does the “silent cost” of automobile manufacturing eat up profits?
In 2023, a German luxury car company suffered a full-year loss of up to US$2.8 million due to mismatched parts on the production line (Source: Automotive News Europe). What’s more fatal is that the failure rate of traditional barcodes in the oily environment of the stamping workshop is as high as 32%, and in the high-temperature paint baking process in the paint shop, the shedding rate of QR code labels even exceeds 45%.
These hidden costs have driven global automakers to accelerate the deployment of RFID technology:
An automobile factory achieves 100% parts traceability through RFID, reducing assembly errors to zero .
A certain intelligent new energy vehicle’s mold switching time is shortened by 78%.
Breakthrough 1: Stamping die management – ending the stubborn problem of “die confusion”
Technical solution: Silicone packaging process for oil-resistant labels
Volkswgen Group uses double-layer silicone packaging labels, with DuPont™ polyimide film as the substrate, achieving:
Anti-hydraulic oil permeability increased by 6 times (ASTM D471 test)
Maintain complete data storage under 15MPa stamping pressure (SAE Technical Paper 2024-01-1056)
Implementation effect:
Mold switching error rate reduced from 1.2% to 0%
Single production line saves **$480,000** in downtime costs per year
Breakthrough 2: Paint shop traceability – solving the problem of high-temperature paint label failure
Damage mechanism analysis
Tests at Fod’s plant show that after a 200°C/20-minute paint process, the IC chip damage rate of ordinary PET labels reaches 89% (Source: Fod Internal R&D Report).
Solution comparison
Technical path | Initial cost | Durability | Data capacity |
Ceramic label (RFIDHY) | $3.8/piece | >10 years | EPC 96 bit |
Laser etched QR code | $0.5/piece | 3 months | 80 bytes |
After Toyot plant adopted RFID ceramic labels:
The accuracy of vehicle body traceability increased to 99.97%
Rework cost reduced**$1.2 million/year** (Toyot Production System Case Study)
Breakthrough 3: Welding workshop – accurate positioning in electromagnetic interference environment
GM deployed UHF RFID readers in Shanghai Plant, combined with:
Anti-metal tags (Impinj Monza R6 chip)
Time-slot Aloha anti-collision algorithm
Results:
Under the interference of 2000 ampere spot welder, the reading rate still maintained 98.5%
White body traceability efficiency increased by 40% (GM China Technical Bulletin)
Breakthrough 4: JIT assembly on the final assembly line – RFID-driven zero inventory revolution
The Tesla Austin factory achieved the following through RFID+MES system integration:
The on-board ECU automatically reads the seat tag and triggers the customized software filling
The tire tag is bound to the vehicle VIN code in real time, and the error rate is zero
Data results:
Line inventory is reduced by 62%
Order delivery cycle is shortened to 10 days.
Breakthrough 5: PDI detection – prevent the escape of defects in the “last mile”
Mercdes-Benz plant uses NFC+blockchain solution in the final inspection:
Each bolt torque data is written into the NXP NTAG 424 DNA chip
Blockchain evidence storage prevents data tampering
Quality improvement:
Customer complaint rate decreased by 83%
PDI detection time reduced by 55% .
ROI verification model: three-year cost comparison analysis
Cost items | Traditional model ($) | RFID solution ($) | Difference ($) |
Part mismatch loss | 2,800,000 | 0 | +2.8M |
Label consumables | 150,000 | 480,000 | -330,000 |
System implementation | 0 | 1,200,000 | -1.2M |
Efficiency gain | 0 | +1,750,000 | +1.75M |
Three-year net profit | – | +3,020,000 | – |
Calculation model refers to the Harvard Business Review Manufacturing ROI Evaluation Framework v4.1
________________________________________
[Appointment for free diagnosis] Get your factory-specific RFID cost reduction solution
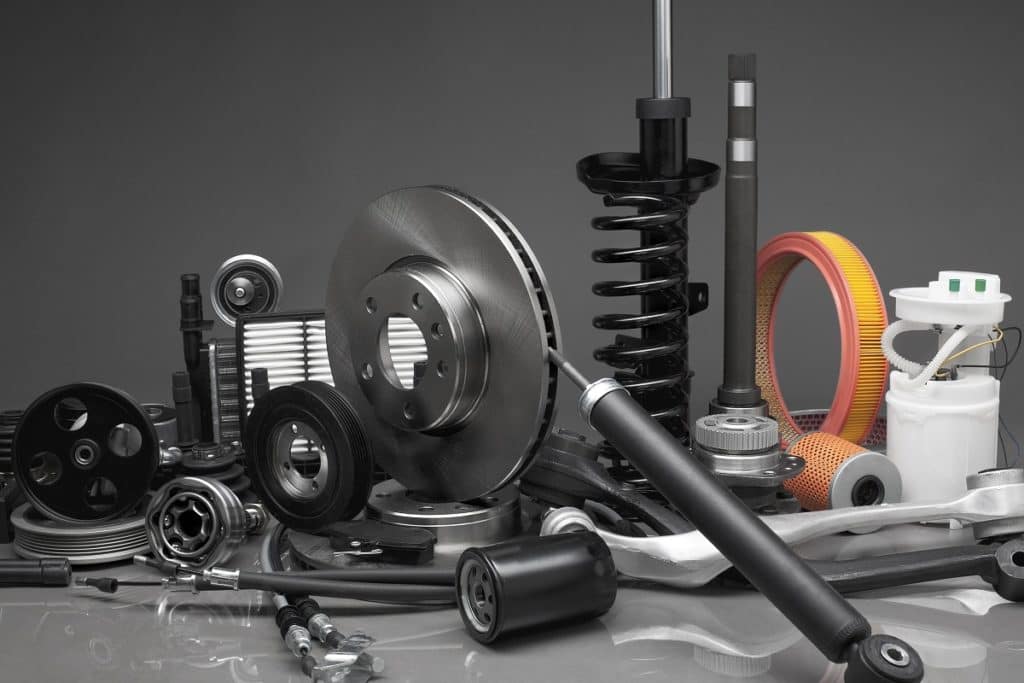